Overview of FHA-E Series Robot Reducer
- Type: FHA-5E~FHA-450E
- Backlash: ≤1-5 Arc.min
- Ratio: 1/35~1/140
- Capacity: 0.1kw~15kw
- Rotation: Shaft run or case sun
- Rated output torque: 60Nm~5100Nm
- Direct output, tight engagement and high precision
Oznaka FHA-E Series Robot Reducer
Description of FHA-E Series Robot Reducer
■The impact load capacity OF FHA-E gearbox is enhanced greatly by adopting load-decentralized technology of multi-gear engagement. While traditional spur gears or helical gears must withstand overload impact due to the meshing engagement of only one tooth.
■ Extremely high efficiency is obtained thanks to the drive of external & internal rollers involved sliding and self-rotation. While in the traditional mechanisms, the unsmooth torque transmission caused by the abrasion or interference of gears.
■ Creative transmission, outstanding advantages
FHA-E Series Robot Reducer provides all the advantages of harmonic gearbox negative the shortages of flexspline.
Without increasing the stages of the reducer, FHA-E robot gearbox can provide high ratios due to the planetary gear drive. And cycloid drive provides high loading capacity without obvious vibration.
■ High efficiency with low sliding loss
All sliding elements consists of roller. When the roller is rolling, sliding is also involved, and therefore the mechanism loss is nearly ignored and gained superior high efficiency up to 95% under only one stage reduction.
■ Smooth operation with low noise
FHA-E Series Robot Reducer provides multi-teeth meshing engagement, at the same time, counterbalanced twin-disc construction of offset vibration, high overlap-coefficient, and roller contact with suitable gap to avoid the interference like gears, which could reduce the noise and vibration effectively.
■ High precision with low backlash
Almost zero backlash of FHA-E robot reducer thanks to the multi-teeth meshing engagement, and therefore the transmission deviation is only 25% of the traditional gear reducer.
■ High torque output due to long diameter of wave exciter
The higher torque of FHA-E robot reducer due to the bigger diameter of rolling wave of roller transmission than traditional disc because of the regular feature of the rolling wave.
■ Compact structure with high ratio
Single stage FHA-E robot gear can achieve high ratio because the quantity of rollers on the roller disc is equal to ratio. Output shaft and input shaft of FHA-E robot reducer are in line, the structure of which is reinforced and space-saving, thus the dimension is more compact under the same reduction ratio of gear reducer and worm reducer.
■ Multi-teeth engagement contribute to high loading capability
Compared with one tooth meshing of the worm gear reducer or gear reducer, FHT-A robot gearbox is featured with 50% rollers meshing engagement simultaneously of twin-disc roller mechanism, therefore the load capacity is higher than traditional gear reducer.
■ Roller tooth contribute to long service life
Overall robust mechanism, free of maintenance and long service life due to the creative roller drive, outstanding technology and process, special roller outline without broken teeth.
■ Better economic benefit due to low energy consumption
FHA-E robot reducer features of high torque output, high efficiency, low operation load, low energy consumption and higher economical benefit.
■Hollow design for direct output
FHA-E RV reducer is designed friendly with hollow shaft and allows to array the routing hydraulic tubes and electrical cable through the FHA-E reducer. And it is easy to mount the motor through coupling and motor flange.
Model | FHA-5E | FHE-7E | FHA-25E | FHA-45E | ||||||
Rotation | Shaft Run | Case Run | Shaft Run | Case Run | Shaft Run | Case Run | Shaft Run | Case Run | ||
Ratio | 40 | 41 | 40 | 41 | 40 | 41 | 35 | 36 | ||
50 | 51 | 50 | 51 | 50 | 51 | 40 | 41 | |||
* | * | 59 | 60 | 60 | 61 | 50 | 51 | |||
* | * | * | * | * | * | 59 | 60 | |||
* | * | * | * | * | * | 79 | 80 | |||
Rated ouput torque | Nm kgf-m | 60 (6.1) | 83 (8.46) | 245 (25) | 460 (46.8) | |||||
Acceleration&braking torque | Nm kgf-m | 97.5 (9.9) | 136 (14) | 515 (52) | 1158 (118) | |||||
Instant Max.allowable torque | Nm kgf-m | 245 (25) | 415 (42) | 1000 (102) | 2300 (234.4) | |||||
Rated input speed | Nr (rpm) | 2000 | 2000 | 2000 | 2000 | |||||
Rated lifetime | Hr | 6000 | 6000 | 6000 | 6000 | |||||
Allowable Max.input speed | Nmax (rpm) | 3000 | 3000 | 3000 | 2500 | |||||
Tilting stiffness | Nm/arcmin kgf-m/arcmin | 82 (8.3) | 117 (12) | 372 (38) | 931 (95) | |||||
Torsional stiffness | Nm/arcmin kgf-m/arcmin | 18 (1.83) | 20 (2) | 49 (5) | 108 (11) | |||||
Max.lost motion | (arcmin) | <3.0 | <3.0 | <3.0 | <3.0 | |||||
Angle transmission error | ATE (arcsec) | 40 | 80 | 40 | 40 | |||||
Backlash | Standard backlash | (arcmin) | <5.0 | <5.0 | <5.0 | <5.0 | ||||
Precision backlash | <3.0 | <3.0 | <3.0 | <3.0 | ||||||
High precision backlash | * | * | * | <1.0 | ||||||
Max.tilting torque | Nm kgf-m | 282 (28.8) | 392 (40) | 1764 (180) | 3332 (340) | |||||
Rated radial force | Nm | 118 | 196 | 882 | 1666 | |||||
Max.axial force | N | 885 | 1470 | 3920 | 5194 | |||||
(I=GD2/4) Input inertia Kg-m2 | 1.65x10-6 | 2.60x10-6 | 1.08x10-6 | 4.50x10-6 | ||||||
1.46x10-6 | 1.85x10-6 | 0.65x10-6 | 3.75x10-6 | |||||||
* | 1.66x10-6 | 0.45x10-6 | 2.4x10-6 | |||||||
* | * | * | 1.75x10-6 | |||||||
* | * | * | 2.4x10-6 | |||||||
Weight | KG | 4.5 | 8.5 | 12 | 32.5 |
Rotation | Shaft Run | Case Run | Shaft Run | Case Run | Shaft Run | Case Run | Shaft Run | Case Run | ||
Ratio | 50 | 51 | 50 | 51 | 59 | 60 | 59 | 60 | ||
60 | 61 | 60 | 61 | 79 | 80 | 79 | 80 | |||
79 | 80 | 79 | 80 | 99 | 100 | 99 | 100 | |||
99 | 100 | 99 | 100 | 119 | 120 | 119 | 120 | |||
* | * | * | * | * | * | 139 | 140 | |||
Rated ouput torque | Nm kgf-m | 1400 (136) | 1615 (165) | 3595 (366) | 5100 (520) | |||||
Acceleration&braking torque | Nm kgf-m | 2083 (212) | 4043 (412) | 7963 (812) | 11025 (1125) | |||||
Instant Max.allowable torque | Nm kgf-m | 4155 (423.5) | 8075 (823) | 17975 (1830) | 25500 (2600) | |||||
Rated input speed | Nr (rpm) | 2000 | 1500 | 1500 | 1500 | |||||
Rated lifetime | Hr | 6000 | 6000 | 6000 | 6000 | |||||
Allowable Max.input speed | Nmax (rpm) | 2500 | 2500 | 2000 | 2000 | |||||
Tilting stiffness | Nm/arcmin kgf-m/arcmin | 1176 (120) | 2940 (300) | 4900 (500) | 7448 (760) | |||||
Torsional stiffness | Nm/arcmin kgf-m/arcmin | 196 (20) | 392 (40) | 980 (100) | 1176 (120) | |||||
Max.lost motion | (arcmin) | <1.5 | <1.5 | <1.5 | <1.5 | |||||
Angle transmission error | ATE (arcsec) | 40 | 40 | 40 | 40 | |||||
Backlash | Standard backlash | (arcmin) | <4.0 | <4.0 | <4.0 | <4.0 | ||||
Precision backlash | <2.0 | <2.0 | <2.0 | <2.0 | ||||||
High precision backlash | <1.0 | <1.0 | <1.0 | <1.0 | ||||||
Max.tilting torque | Nm kgf-m | 4312 (440) | 7840 (800) | 14112 (1440) | 17640 (1800) | |||||
Rated radial force | Nm | 2156 | 3920 | 7056 | 8820 | |||||
Max.axial force | N | 7840 | 14700 | 19600 | 24500 | |||||
(I=GD2/4) Input inertia Kg-m2 | 5.65x10-5 | 1.9x10-4 | 6x10-4 | 9x10-4 | ||||||
4.40x10-5 | 1.8x10-4 | 5.4x10-4 | 7.3x10-4 | |||||||
3.53x10-5 | 1.78x10-4 | 4x10-4 | 6x10-4 | |||||||
2.63x10-5 | 1.51x10-4 | 2.8x10-4 | 4.8x10-4 | |||||||
* | * | * | 4.2x10-4 | |||||||
Weight | KG | 32.5 | 37 | 65 | 81 |
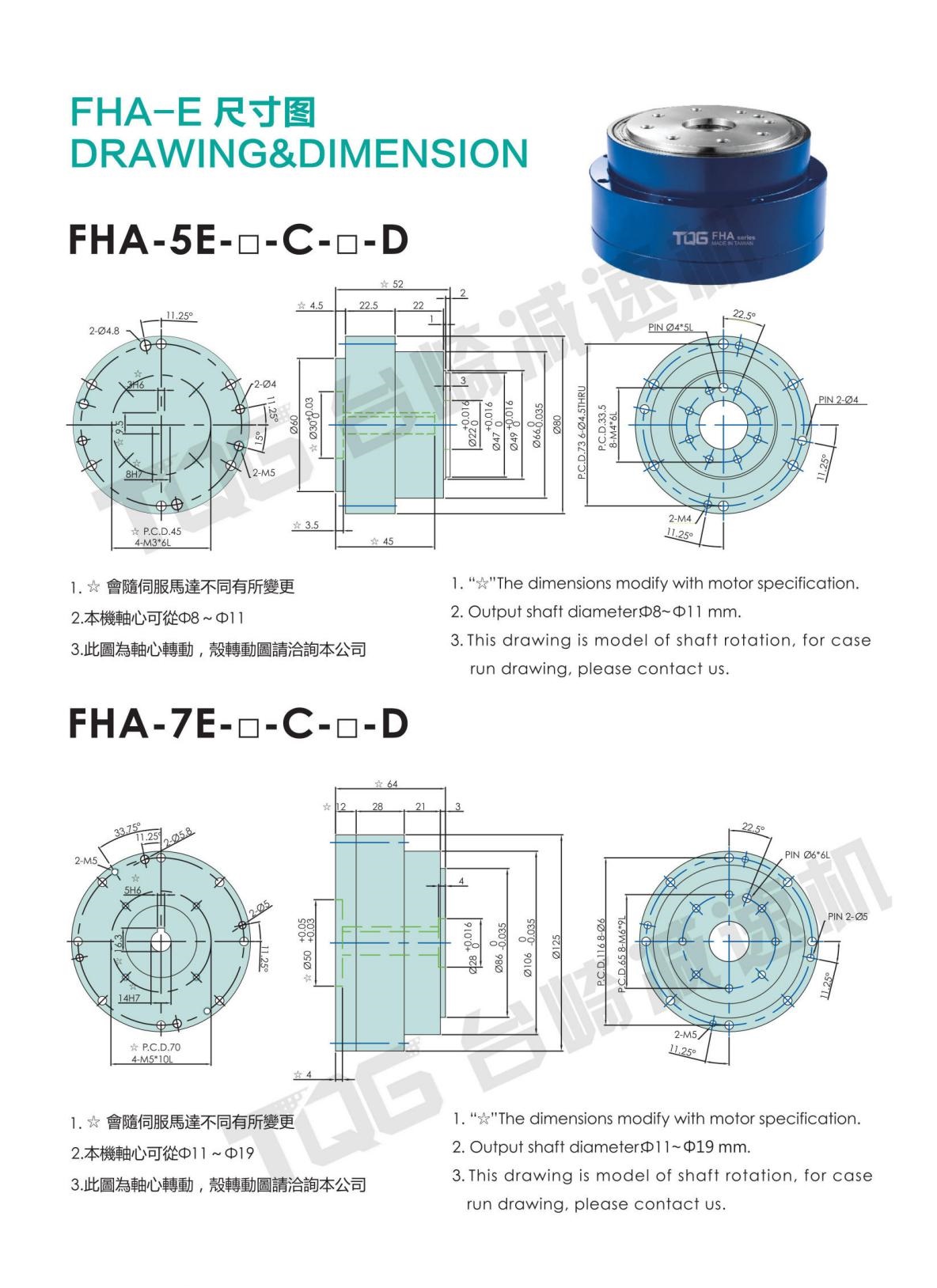
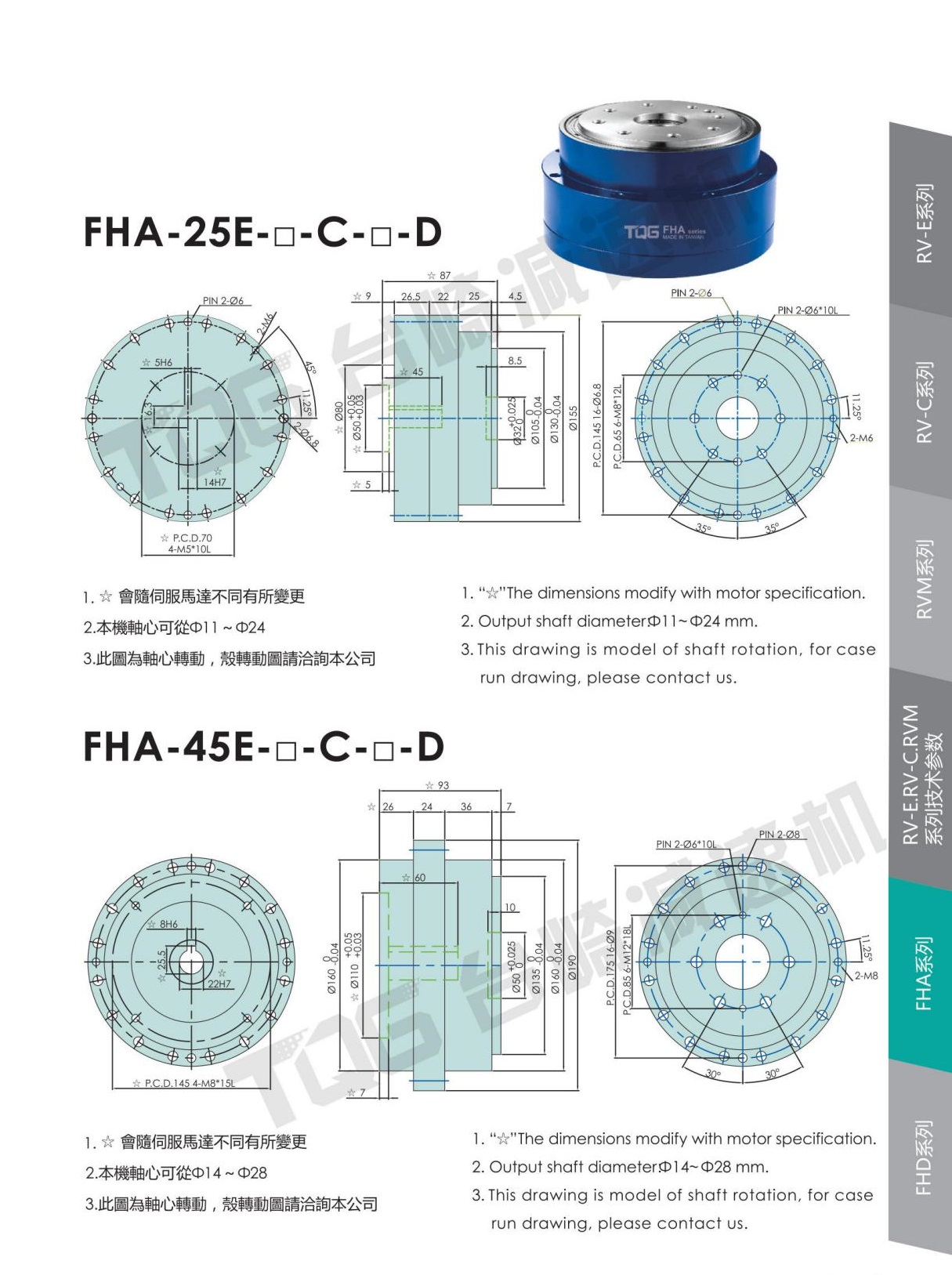

